Good manufacturing practices rest solidly on documentation, documentation, and more documentation. You could be (and possibly are) doing everything right, and ensuring that your product is of the highest possible quality each and every time. But is it all documented? Without accurate and detailed documentation, your GMP will never be fully in place.
While it does take some time to get all your procedures and recipes written down, and some effort to ensure that what’s written down is actually followed, there are a few things that can make the process (and the final result) a little easier.
1. Use Binders
Simple 3-ring binders are a great way to store your procedures, master formulas, specification sheets, and batch records. When your records are in binders they can be quickly found and rreferenced. The binders store nicely on a shelf for ready access and you can easily add new materials.
To start with, one binder can probably hold all of your documentation; just use binder tabs to separate the sections. As you get more documentation in place, you can easily separate the different types of documents into individual binders.
2. Use Sheet Protectors
Sheet protectors are wonderful things! They keep the paper protected, so you can have your materials right there in your work space while you are making your products or handling your ingredients without fear of damaging the papers when handling them.
If you use sheet protectors, be sure to get the “oversize tabs” for the binder, so the tabs stick out enough to easily see them.
3. Set Up Numbering Systems
Numbering your different types of documents makes them easier to refer to and keep in order. In my book, Good Manufacturing Practices for Soap and Cosmetic Handcrafters, I recommend using a letter-and-number system for each type of document. For example:
- Standard Operating Procedures: “SOP” followed by sequential numbers; e.g. SOP-0001, SOP-0002, etc.
- Specification Sheets: “SPEC” followed by the type of item, followed by an identifiable abbreviation; e.g., SPEC-OIL-PALM, SPEC-EO-LAV, SPEC-BOT-COSMO-BL-4.
- Lot Numbers (for incoming materials): A letter prefix to identify the type of item, followed by the year and then a sequential number with leading 0’s; e.g., EO120001, BOT120001, etc.
- Master Formulas: Create a letter/number code to identify the product, then a suffix for the variations/scents of the product; e.g., MF-LTN-LAV, MF-SOAP-TEATREE, etc.
- Batch Numbers: Use the date created (year, month, day) and with a letter if more than one batch is made in a day; e.g. 240703-1, 240703-B.
Other numbering systems will work as well, the key here is to decide what the numbering system(s) will be and then stick to them.
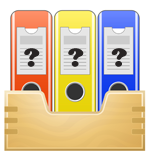
4. Keep Logs
Logs are like indexes to your documents. Every time you create a document, add the name and information to a log sheet; when you make a batch, add it to the log sheet. That way you have a simple and concise place to look if you need a document.
The log can contain whatever information you want in addition to the number and name of the document. For batches, you might want to include the number of products made or even the cost for the batch or per item. For Standard Operating Procedures, you might want to keep the name of the computer document file.
5. Standardize Formats
It’s always easier to find and read your documentation if it is in a standardized format. It’s also easier to write your documents if you have a standard format to follow.
One of the easiest ways to do that is to set up a template in your word processing program. When you’re ready to write a new Standard Operating Procedure, it becomes a matter of just filling in the blanks with the right information (rather than having to start from scratch every time).
You’ll need different formats for each of the different types of documents.
6. Standardize File Names
Assuming at least some computer literacy, most of your documents will be created using some sort of word processing software. As you write the documents, give them standardized names and file them logically on your computer in a way that makes them easy to find. If they are easy to find, they will be more likely to be updated when needed.
I suggest a folder named “GMP” or “good manufacturing practices” and then sub-folders under that for each type of document. Document names should be the document number, followed by a brief descriptive title, e.g., /gmp/sop/SOP-0001-Cleaning.
7. Record Reasons for Changes
When you decide you need to change a document, make sure you write down (on the document) when and why you changed it. That keeps a running history and will make it easier to go back and figure out what’s what if you ever need to.
Also be sure to keep the older, original version of the document.
8. Print Checklists in Advance
Some of the documents you’ll need are checklists. When you receive incoming materials or ingredients, you should have a checklist to verify that the item(s) are up to spec, and when you make a product, you’ll need a batch record (which is a sort of checklist) to record what was done. Some SOPs also have checklists to document the completion of the procedure.
It’s easier if you print your checklists in advance (at least a copy or two), so you can complete them easily and quickly when needed, without having to go back to your computer, find the file, and print your paperwork.
Leave a Reply