Last week The Nova Studio posted a great post, Why You Should Care About Lot Numbers, detailing their experiences on finding out that the San Francisco Herb & Natural Food Company in Fremont, CA had a bad rodent infestation & was recalling over a dozen of their products that may have been infested with droppings. The news report on it includes a list of the recalled items; the business is indefinitely closed.
Important Note: This is NOT the reputable San Francisco Herb Company, located in San Francisco and a reliable provider of herbs and spices to many people and companies that make handcrafted soap and cosmetics.
It can be quite a scare if you think you could possibly have a contaminated ingredient! Luckily, The Nova Studio had taped the labels on their containers of herbs, which documented the source, along with the supplier’s batch numbers (and none of their herbs were from the supplier in question).
Lot Numbers Are Required by GMP
Imagine how you’d feel if you had purchased some items from the company in question, and had spearmint leaves in your inventory. If didn’t know where they came from and what batch(es), it would mean that you’d have to toss all the spearmint leaves AND any product made from them, and you might even need to contact customers who had purchased products containing those spearmint leaves. A nightmare, to say the least.
On the other hand, if you have records of exactly where your spearmint leaves came from (and the batch numbers for them) you’d be able to tell right away if you had a problem or not.
And therein you have a real-life example of why keeping lot numbers for all incoming ingredients and materials is a key (and required!) part of GMP.
Recording Lot Numbers
Every time you receive an incoming ingredient or material (including packaging materials) it should be logged somewhere. The information to keep includes the item, supplier, date, the suppliers batch number (if any), and the lot number you assign to the batch of incoming materials (which could be either the supplier’s batch number or one that you create).
You should also note the status of the item (accepted, rejected, on hold). The status is determined after you check the item and make sure that it conforms to your required specifications, as detailed in your own Specification Sheet for the item.
The log can be kept simple, on a paper form or a spread sheet, just so long as it is kept up to date and easily accessible. Here’s an example of a sample form:
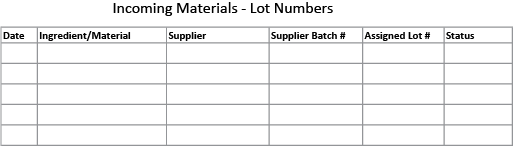
Labeling Your Inventory
When you put the incoming materials or ingredients in your inventory, it’s important to ensure that it is properly labeled, so you can tell what’s what at a glance.
I suggest a label that looks something like this:
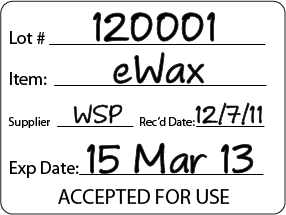
The label should be large enough that you can see it at a glance.
Using Ingredients in Batches
Whenever you use an ingredient in a batch of product, the lot number should be noted. That way if you ever need to, you can go back and determine which batches used a particular product lot.
Good Manufacturing Practices Help You
Keeping lot numbers for all your incoming ingredients and materials, and noting when those ingredients and materials are used in product batches, is required by GMP. But even more importantly, it’s a way to give you peace of mind if you ever find that you have received potentially contaminated product.
GMP is all about making sure that your products are of the highest possible quality, every batch, every product, every time. And that’s what you want, right?
If you have questions about what GMP requirements are (or how to implement them) feel free to submit your question and/or purchase Good Manufacturing Practices for Soap and Cosmetic Handcrafters from Amazon using the button below.
Leave a Reply